As technology continues to evolve, so too do the components that make it work. One of these components is ceramic bearings, which are found in a variety of modern machinery.
Ceramic bearings have revolutionized engineering thanks to their durability and precision – two qualities that enable machines to operate with greater efficiency and accuracy than ever before. This article will explore the role ceramic bearings play in today’s engineering industry, examining their history, uses, and potential for future development.
With advancements being made every day, engineers must remain on top of new developments to ensure their projects function at maximum effectiveness. By understanding the importance of ceramic bearings and how they can be used effectively within modern machinery, engineers can stay ahead of the curve when it comes to manufacturing solutions.
Benefits of Using Ceramic Bearings in Modern Engineering

Ceramic bearings have become an integral part of modern engineering, providing several benefits for applications in machinery. The use of ceramic bearings can provide increased longevity and reliability to equipment while reducing overall energy consumption.
By using ceramic materials instead of traditional metals, engineers can reduce vibration and noise levels as well. Ceramic bearings also offer improved performance in extreme temperatures or environments with high levels of contamination or debris.
In addition to these advantages, ceramic bearings help increase the efficiency and accuracy of operations by offering smoother motion than traditional metallic counterparts. As such, their use is becoming increasingly prevalent across many industries where precision matters most.
Further savings are realized through extended service life that reduces maintenance and replacement costs over time as well as more efficient energy usage due to reduced friction between moving parts that require less horsepower to operate effectively. All these factors contribute greatly towards making ceramic bearing technology a vital component in modern engineering today
Advantages and Disadvantages of Ceramic Bearings
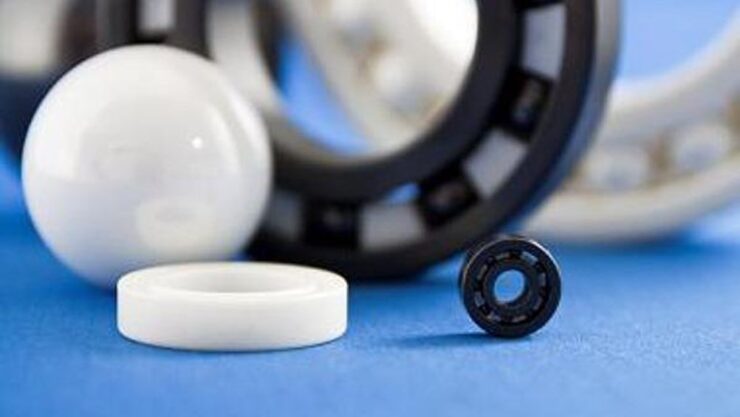
Ceramic bearings offer a range of advantages and disadvantages for use in modern machinery. On the plus side, they are lighter than steel bearings, which can reduce machine vibration and thus improve efficiency.
Additionally, ceramic bearings have higher temperature resistance than their steel counterparts, making them suitable for machines used in extreme temperatures. Ceramic bearings also have a longer lifespan as they do not corrode or rust like their metal counterparts.
On the downside, ceramic bearings tend to be more expensive due to their specialized components and manufacturing process. Additionally, since ceramic is less hard than steel it cannot withstand as much force or pressure before breaking or wearing down over time.
Furthermore, some materials such as aluminum oxide are brittle and may break if mishandled or exposed to sudden shock loads; this fragility makes them unsuitable for certain industrial applications where high levels of reliability are required. Finally, because ceramic does not conduct electricity well enough compared to its metal counterpart it is not recommended for electric motors unless additional insulation measures are taken into consideration before installation
Conclusion

Ceramic bearings have played a major role in engineering evolution over the past few decades, revolutionizing modern machinery. They are lighter and more efficient than traditional steel bearings, providing machines with increased speed and longevity. Moreover, ceramic bearings can be used in environments where steel would corrode or wear down quickly due to their excellent strength and resistance to chemical deterioration.
With such impressive qualities, it’s no wonder ceramic bearings have become an essential component of so many industrial-grade motors and mechanical systems around the world.