For sustainment in today’s cut-throat emerging markets, implementing new technologies in the manufacturing process is the only way of survival for the manufacturing companies. It helps them in knowing where the money invested gets utilized and assists in finding any incompetence in the present company’s operational policies and any wastage of raw materials.
Every manufacturing company is always trying to find various means to cut down their operational costs and increase profits, and in the year 2024, this is still their main criterion.
Even though project management sounds complicated in the industries involved in manufacturing, taking help from manufacturing project management software tools helps manufacturing companies make optimal use of the resources available through implementing proper planning. The software supports the companies in effectively customizing the required specification in the tool as per the industry’s requirements.
These tools are explicitly designed to help companies allocate resources to manage relevant projects effectively and generate customizable intelligence reports through creative collaboration and data evaluation, allowing focus on tasks ahead.
Understanding The Term Project
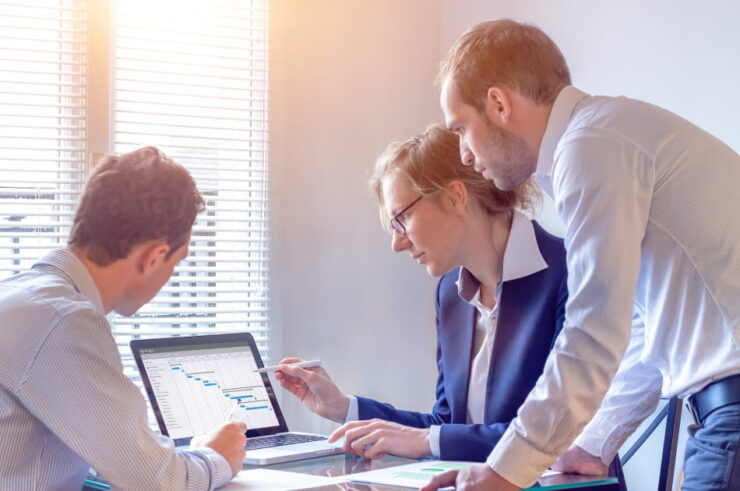
To achieve a specific set of goals, a series of tasks must get completed to reach it, known as a project. A project could be anything from implementing effective measures for the optimal use of raw materials or even procurement and erection of machinery at the factory, building a house, painting, and many others.
The most common thing in any project is a requirement to plan before tasks get set to complete. This planning phase gets done to finish the project most cost-effectively.
Since planning requires much effort and organizational skills, effective project management can significantly help the planning process.
Project Management
Project management is known as adequately maintaining the project’s schedule by effectively processing and implementing various small-time tasks that help keep the project on the right track and get completed as per schedule. It helps structure a trackable way that helps in proper follow-through to reach the deadline on time.
It uses various tools, techniques, methods, and software to complete a project by meeting the product outputs labored to a budget within the prescribed time limit.
Strategies For Effective Project Management
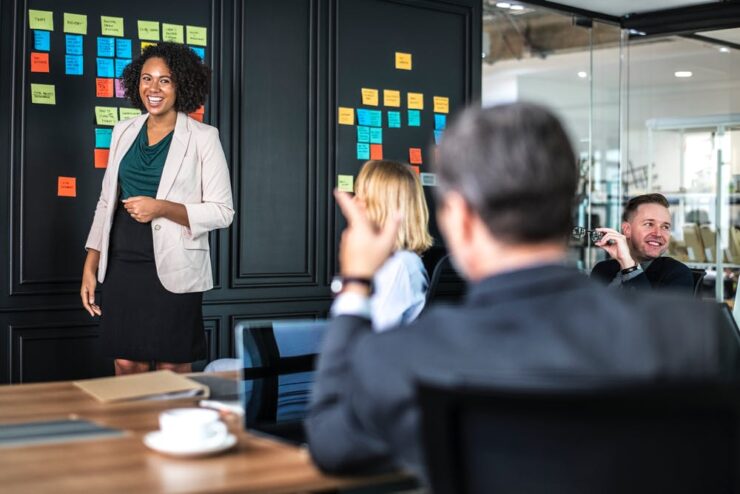
Effective project management has a set timespan for product output, and it involves management skills for maintaining people, technical skills, and general awareness to spot suitable business needs. Achieving any goal for any company or individual could be completed cost-effectively only with project management. Without compromising the quality, a few strategies for practical project management are,
Computerize The Workforce
In today’s digital world, going paperless is the only way to work in a cost-effective, environmentally friendly way.
After the digital transformation, even if the company implemented the paperless policy, there could still be few departments that keep paper.
Since the industrial revolution over a century ago, the digital process has benefited manufacturers by guiding them digitally to track on-time progress at their factory plant and have proper effective communication with production staff.
The process of computerizing cut cost in areas such as
- Through real-time trace marks, reducing the defects of final products.
- Implementing practical, reliable training of management staff and workers increases production, which helps in improving the accuracy of decision-making at the operational level.
- Effective capture of tribal knowledge (Unwritten knowledge like passwords, abstract data, and others) helps reduce the training time.
- Reducing the skill gap among the workforce helps strengthen them.
Practice Improvement
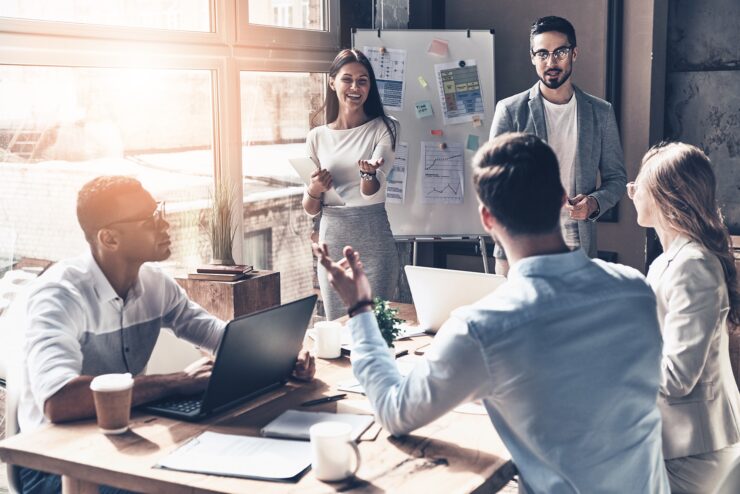
Implementing lean manufacturing inventiveness like Six Sigma or Kaizen techniques helps continuous improvement in the workforce. Developing the employees’ work routine by documenting standard operating procedures solves complex work routines.
Following and implementing the local rules and regulations, work personnel safety standards, various environmental standards, and ISO certification help certify the company and its products under international standards.
Establishing performance indicators as a key to trigger the company’s members will directly impact the business. It helps the staff members to follow the right direction by interacting with all the departments in the organization.
Recycling The Waste
Reducing waste and reusing and recycling should be the motto of all manufacturers. All factories give waste output, and that is normal.
Factories with excessive scrap material, such as debris and defective post-production products, can prove costly for manufacturers. The main reason is that these manufacturing plants do not have a strict quality control department. All the extra effort and materials wasted drain the profits from the factory.
But the development of Internet of Things (IoT) technologies has brought a different outlook to reducing bad habits in the production phase in a factory. It helps identify the defects using sensors and monitors the quality of the final product through automated calibrations. Real-time alerts get sent out when there is a breakdown in machinery or the production process, which helps the technical staff to rectify the process on time without further escalation.
The errors that translate to defects in the final production unit are caught early, thus reducing the quantities of defective products.
Supply Chain Management
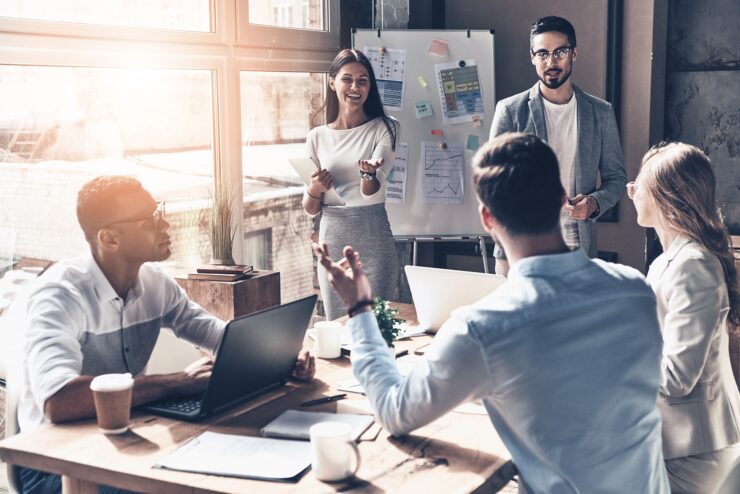
The bottom line of the production control unit takes a hit if the supply chain process and other relevant protocols aren’t managed and monitored.
Sometimes considering the market scenario of fluctuation of raw material prices, purchase departments purchase an extra supply of raw materials as countermeasures.
The outcome is that it is indeed a costly practice for the manufacturer. The implementation of project management software and various other tools can help in the coordination of the operations in the plant by giving accurate predictions that will help save costs.
With this, the manufacturers can have enough inventory in their store with a timed re-order process.
Workforce Health & Safety
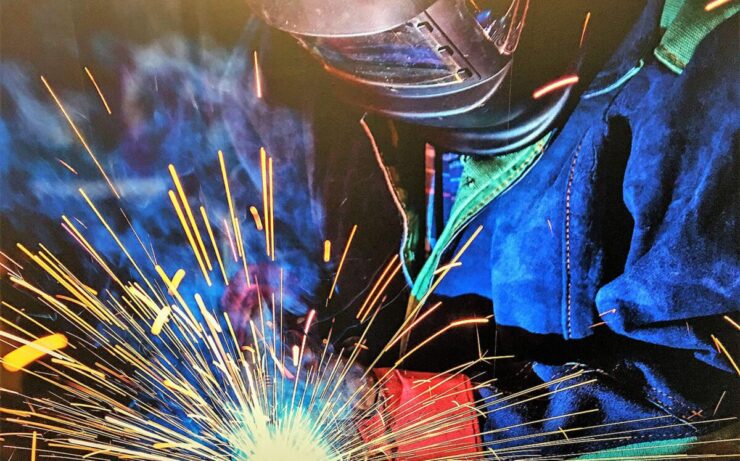
Due to skilled work, like welding and other applications, handling dangerous chemicals, and operating large equipment, manufacturers deal with workplace situations that cause danger.
An injury-prone workforce will increase expenses with absenteeism, slow production, boost production costs, and low workman morale. Apart from that, the insurance cost will never reduce the expenses.
Factories nowadays should be proactive with the safety and health of their workforce if they want to overcome labor shortages and skill gaps in the force.
Conclusion
There is no one solution to cut down the cost and increase profitability. When taken seriously and implemented, it is a series of actions that will significantly impact the company’s financial health.
Companies should use intelligent technology to cut energy costs, become proactive, and automate manual, repetitive processes. Apart from that, implementing new protocols effectively and keeping track of key performance indicators are a few strategic decisions that the project management team of a manufacturing company should implement to save costs in 2024.